Labels in the logistics industry
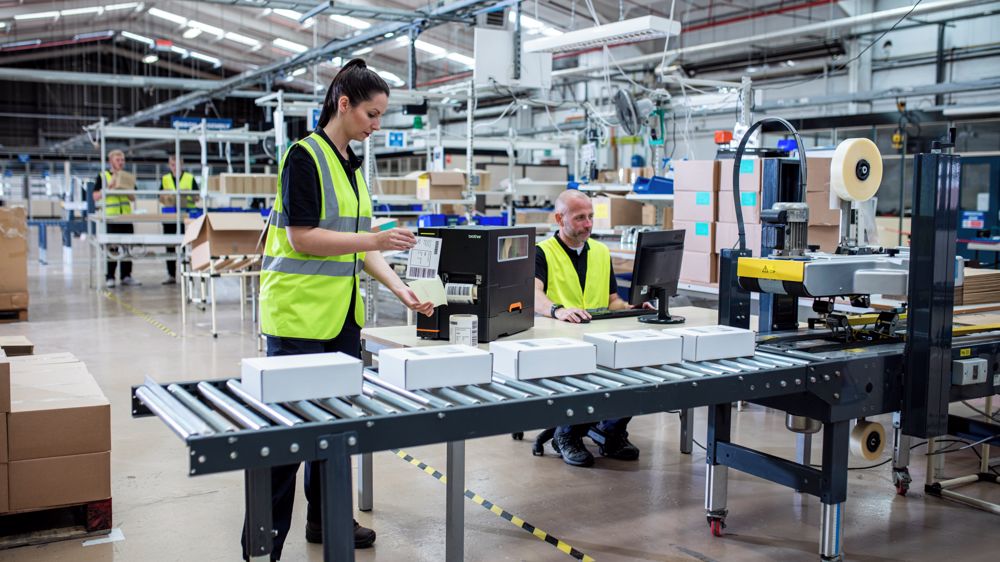
Australian warehouse managers face a series of challenges when it comes to the efficiency of their business processes. Workflows are often bogged down, with extra time spent processing or resolving human errors caused by manual inventory tracking methods.
A comprehensive warehouse barcode label solution can streamline operations and reduce the productivity loss associated with inefficient methods. This article will showcase how deploying a labelling system can improve your warehouse and logistics workflows.
Common challenges of warehouse labelling
Some of the more prevalent and recurring challenges when labelling in a warehouse environment include:
- Incorrect label positioning
- Damaged labels
- Unscannable labels
- Poor print quality
- Immobility of the label itself
Damaged and unscannable labels impact the traceability of your products and can cause disruption across the entire supply chain. Gaps in inventory data and misaligned ordering schedules associated with rectifying errors are just some of the vulnerabilities attributed to deploying a poor labelling architecture. Other consequences of improper or insufficient warehouse labelling include:
- Higher cost of labour: When products/pallets aren’t labelled correctly it can disorganise and throw off critical warehouse workflows, such as inventory management, scheduling and delivery. Correcting these mistakes increases labour costs and sidetracks productivity, which ultimately frustrates the customer
- Poor traceability: Labelling mistakes make it more difficult to locate, track and identify products. This is especially true when executing product recalls, which can be time-consuming and tedious to resolve without the right technology
- Potential loss of business: If poor labelling can result in frequent mistakes or a frustrating client relationship you may lose credibility. In turn, you can lose customers and business partners if mistakes aren’t rectified and prevented

Key considerations when labelling in the warehouse
Introducing or re-deploying a warehouse labelling strategy should include a few important elements. If you’re looking to improve traceability and transparency across the supply chain, consider the following questions:
- What is being labelled? By first answering this question, you’ll set yourself down the right path when selecting the optimal label for any given application. As reported by Supply Chain Management Review, labelling accounts for less than five per cent of total warehouse cost but is one of the most important aspects of daily operations. From small labels that identify individual parts, to barcode labels that link to inventory management systems, these versatile solutions provide visibility for all warehouse processes
- How long does the label need to last? Certain warehouse labels may only need to last a few days, or at least until they’re received by the customer. For pallets containing products waiting to be shipped, a scannable label may only need to last a day or two before the products are loaded onto the various trucks that will facilitate their delivery. Others may need to last years, such as those attached to bins or warning signage. For products that are shipping by land, sea or air to waiting consumers all over the world, a durable label is needed to successfully complete the journey
- Where on the warehouse floor will the label be printed? This can help determine the type of device you need. Certain areas of the warehouse may need to print labels in large quantities at one time. The goods reception area oversees the inspection of received items. In the event that a product is defective or damaged, a new label classifying its status allows these items to be sent to their proper location. Given the amount of product that can flow into a goods reception area everyday, a print solution needs to be capable of keeping pace. Devices like the Titan TJ-4420TN Industrial Printer can produce 10,000 paper documents per day. For print jobs that only require a few copies, areas like overflow control stations can use desktop label printers like the PT-P950NW to assign barcodes to bins, totes & storage containers
- What type of label is required? Some warehouse applications are best served by a particular type of label printer, such as one that is mobile or one that produces durable labels
How to label throughout the warehouse floor
Labels are utilised in different ways across the typical warehouse workflow. Brother offers durable, versatile labelling devices and solutions designed to increase productivity and streamline your business processes.
From dock to stock, here’s how you can utilise today’s labelling technologies in order to accelerate your warehouse workflow:
Receiving
- Barcode labels
- Receipt labels
- Product ID labels
Storage
- Rack labels
- Storage labels
- Shelf labels
- Pallet labels
- Container labels
Picking
- Order preparation labels
- Product ID labels
- Shelf labels
- Barcode labels
Packing
- Shipping labels
- Packing labels
- Tracking labels
Today’s fast-paced business environment requires line-of-sight into tracking methods and expedited systems that can get your inventory out the door faster. Brother labelling solutions support and add value to a wide variety of warehouse and logistics applications.

5 benefits of a properly labelled warehouse
Re-aligning your labelling strategy can provide a significant boost to your warehouse workflows. Here are five benefits that an effective labelling system can offer:
- Reduction in errors: The durability of Brother labels printed on TZe laminated tape hold up to the rigours of the supply chain, ensuring scanned products are instantly updated to your inventory management systems. This ensures you’re never in the dark regarding the status or location of your products
- Smarter picking: Scannable barcodes provide line-of-sight into picking quantities and reduce downtime associated with manually logging inventory quantities
- Simplified inventory management: Consolidate your business processes under one platform thanks to Brother’s Software Development Kits (SDKs). Integrate your mobile print and labelling devices with existing software thanks to the simple, inexpensive and reliable means of interfacing with your new labelling system
- Higher SKU visibility: The one-touch scan capabilities on select portable scanners provides your workforce with the dexterity to perform product tracing and inventory management from anywhere on the warehouse floor
- Improved warehouse efficiency: Your workflows will benefit from a labelling architecture that updates inventory tracking systems in real time, thanks to the connectivity of Brother mobile labellers
Brother offers a range of labelling and scanning solutions designed to provide transparency and traceability across the entire supply chain. To bring out the best in your business with modern labelling solutions, contact Brother today.
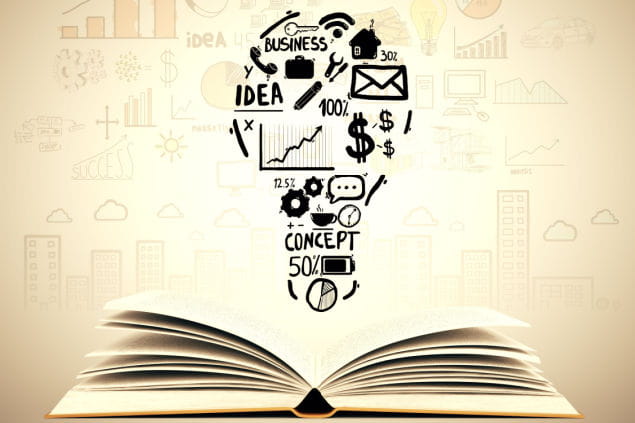
Resource Library
Be the first to receive exclusive offers and the latest news on our products and services directly in your inbox