4 uses for mobile printers in the supply chain
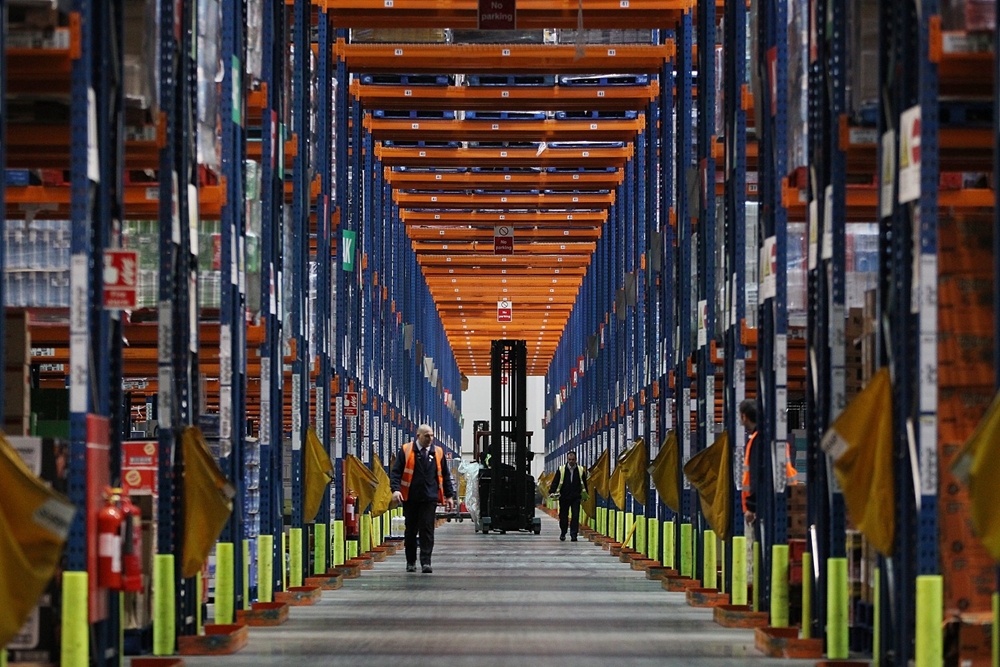
Pressure for promptness in the supply chain has only increased over the past few decades. Today, nearly three-quarters of all Australian households shop online, amounting to 10% of all retail spend, according to the 2019 eCommerce Industry Report from Australia Post. Within the next few years, online shopping is expected to increase to 12% of all spending.
Not only are consumers’ shopping habits changing in light of increased e-commerce capabilities, but so are their expectations. Fast shipments are becoming the norm, and next-day deliveries increased 31.7% between 2017 and 2018.
While expedient shipping is pertinent, accurate delivery expectations are more important; 13% of consumers said they’d never shop from a retailer again if an order arrives late.
What all these trends mean for retailers and logistics providers is that speediness and accuracy are key to customer satisfaction. The supply chain must evolve to meet consumer expectations.
Mobile printers represent an opportunity for companies to make their processes more efficient, enabling workers to expedite important operations and access necessary information much quicker. This technology can assist workers at multiple stages in the order fulfillment and delivery processes. This article will explore four specific ways mobile printers can make the supply chain more efficient.
1. Inventory management
Keeping accurate inventory records has always been essential for retailers. In the age of e-commerce, instantaneous information about exact quantities and locations of certain items is critical.
Effective inventory management begins immediately after items arrive at a warehouse or other location. Labelling each item as it arrives ensures they’re logged in the warehouse management system (WMS), giving as accurate a look into inventory levels as possible. Using barcode or RFID labels provides a real-time view into the journeys of specific pallets, packages and individual items.
2. Picking and packing
The picking and packing processes are perhaps among the most important to optimise when creating a more efficient supply chain. Carefully planning out your warehouse or distribution centre is essential in supporting productive picking and packing activities.
Organisation is key for efficient picking. Having established systems for which SKUs belong where and the best routes for pickers to take during order fulfillment can help reduce the time it takes to assemble each package.
Precise labelling systems using barcoding or RFIDs also help expedite picking and packing operations. When workers fulfill orders, they need to know where each item is located in the warehouse or distribution centre. Being able to look up these locations will allow them to navigate the facility quickly and strategically.
When packing orders, employees should have immediate access to all necessary equipment, including boxes, packing material, and labels. Each shipping label placed on or with a package, or pallet of packages, must be durable, legible, scannable and inclusive of all essential information.
A printing system that can produce high-quality signs, labels and maps can benefit workers immensely when working to improve productivity. Even more helpful are mobile devices that can scan and print information, and help pickers and packers access order information.

3. Reverse logistics
The return process is another important area retailers must consider. Customers prefer to be able to return unwanted purchases easily and inexpensively. Unfortunately, Australia Post’s study found that 34% of consumers said returning products is too expensive.
Retailers can take several measures to make the return process easier and cheaper for customers. One of the best ways to simplify returns is to provide a return label in the delivered package. Even better: If pre-paid postage is included. The packaging that items are shipped out in may also be designed for double use, eliminating the need for customers to seek out a suitable box for their unwanted goods.
Using mobile printers to produce on-demand return labels makes this process easy for packers to carry out. In addition, having the correct information on the outgoing package as well as the return label allows the retailer to track shipments accurately throughout the entire process.
4. Direct store delivery
Direct store delivery (DSD) is a distribution model in which manufacturers deliver their products directly to retailers, rather than working through third-party distributors.
This model gives retailers greater control over their inventory and the flexibility to adjust to changing consumer demands. It also shortens the supply chain, which is especially beneficial when working with perishable goods. For this reason, DSD is particularly popular among food and beverage establishments, such as grocery stores.
One challenge in adopting a DSD model is having a complete view of available inventory in the store. Retailers that don’t have total insight into their inventory may fail to place needed orders, or wind up purchasing excess quantities of certain items.
Mobile printers can help companies keep more accurate records – essential for the retailers receiving goods, as well as the distributors delivering them. By scanning labels immediately upon delivery, everyone is kept in the loop. Plus, this helps to sort, organise and distribute goods quickly and efficiently.
Supply chain efficiency is a multi-faceted goal
There’s not a simple or quick fix to make the supply chain more productive. Instead, efficiency relies on making each stage from the manufacturer to the warehouse to the retailer or end customer as smooth as possible.
Having access to critical information and documentation is a common trend at each of these stages. Mobile solutions that support the quick printing of high-quality labels that are easy to read and scan, allowing workers to look up detailed information, can help cut time and save money.
In the end, empowering employees with the tools and technologies they need to work as productively as possible can be one of the most helpful ways to increase efficiency throughout the supply chain. Contact us to learn about how Brother can help you improve your warehouse or distribution centre.
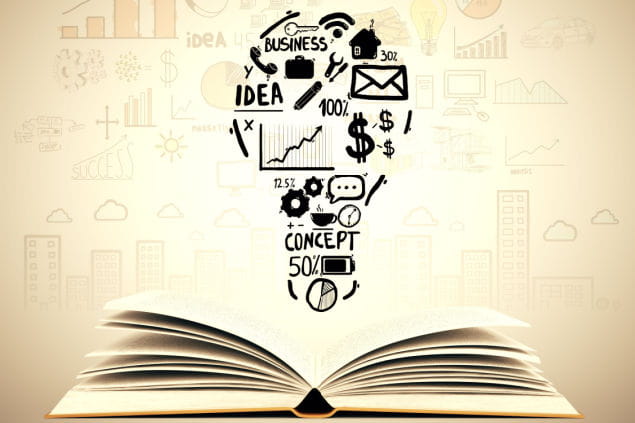
Resource Library
Be the first to receive exclusive offers and the latest news on our products and services directly in your inbox